3.1 Morteros de cemento
Composición
Cemento
Corriente o Alta Resistencia según requisitos de resistencia y velocidad de fraguado.
Arena
Se empleará arena apta para hormigones con tamaño máximo de 2,5 a 5,0 mm, según empleo.
Dosis de Cemento
A falta de especificación se emplearán morteros 1:3 en volumen (1 saco de cemento por 100 litros de arena).
Agua
Potable y/o libre de impurezas.
Dosis: la menor posible compatible con condiciones de colocación.
Aditivos
Expansor para control de retracciones en morteros de relleno.
Plastificante o fluidificante para morteros fluidos de inyección o grout.
Aceleradores de fraguado
Trabajos rápidos de reparación (empleo limitado en contacto con armaduras).
Emulsiones acrílicas
En lechadas de adherencia y aplicación de capas delgadas.
NOTA: En cada caso, respetar dosis e instrucciones de aplicación de los fabricantes.
Resistencias Mecánicas
Deberá ser Igual o superior a la de los elementos que se deben reparar.
Cuando no se especifique se recomienda una resistencia a compresión de 300 kg/cm2.
Bajas Retracciones
Los morteros de reparación o de relleno deberán tener una retracción controlada.
En general se recomienda el empleo de expansores para compensar la retracción plástica y exudación.
Trabajabilidad
Empleo de morteros secos o ligeramente plásticos (baja razón agua-cemento) en todos los casos en que sea posible su aplicación. Cuando se requieran morteros para inyección o grouting emplear aditivos plastificantes o fluidificantes, manteniendo una razón agua-cemento baja.
Adherencia
Emplear productos de adherencia acrílicos o epóxicos.
3.2 Morteros con polímeros
Definición
Son morteros de cemento a los cuales se les adiciona una emulsión de un polímero acrílico o Látex sintético.
Los polímeros actualmente empleados en la elaboración de estas emulsiones son de tres tipos: acrílicos, estireno-butadieno (SBR) y acetato de polivinilo (PVA); estos últimos no son recomendables para aplicación a ambiente húmedo permanente.
Las emulsiones de polímeros tienen dos formas de aplicación características.
Lechadas de Adherencia
Utilizadas como puente de adherencia entre el mortero fresco y la base (mortero, hormigón o albañilería).
Para preparar la lechada de adherencia se mezcla cemento y arena fina en proporción 1:1 y luego se agrega la emulsión acrílica diluida en agua en la proporción indicada por el fabricante, mezclando hasta obtener una consistencia cremosa.
La lechada se aplica con brocha sobre la superficie; el mortero se debe aplicar sobre la lechada fresca antes de una hora.
- Morteros con Polímeros
- La adición de una emulsión acrílica a morteros de cemento mejora considerablemente algunas de sus propiedades:
- Elevada adherencia a la base (resistencia al corte 28 ± 5 kgf/cm2)
- Resistencia a compresión a 28 días: 250 a 450 kgf/cm2
- Resistencia a flexotracción a 28 días: 65 a 100 kgf/cm2
- Módulo de elasticidad en compresión: 250.000 kgf/cm2
- Baja tendencia a la fisuración.
- La dosificación recomendada es de 1:3 a 1:3,5 (en peso) con una razón agua-cemento entre 0.30 y 0.40 (incluida la emulsión acrílica previamente disuelta en el agua).
- Los morteros con polímeros se emplean principalmente en trabajos de reparación y aplicación de capas delgadas.
3.3 Morteros Predosificados
Definición
Existen en el mercado diversos productos preparados en fábrica o en plantas, que se entregan listos para su empleo y sólo requieren que se agregue agua para su colocación en obra.
Ventajas
Productos de fabricación controlada, dosificación en peso, diseñados para fines específicos.
Especialmente adecuados para trabajos de reparación donde se requieren productos de calidad y no existen los medios para una confección controlada.
Tipos
Morteros de reparación de baja retracción: Resistencia a compresión a 28 días entre 200 y 300 kgf/cm2 . Reparaciones en general, albañilerías, hormigones de resistencia moderada <300kgf/cm2.
Morteros de alta resistencia y baja retracción para reparaciones: Resistencia a compresión a 28 días entre 300 y 450 kg/cm2 para reparación de estructuras de hormigón.
Morteros de fraguado rápido: Gran velocidad de endurecimiento para trabajos rápidos. Resistencia a 7 días > 300 kgf/cm2.
Morteros para reparación de hormigones de alta resistencia, con resistencia a compresión a 7 días de 700 kgf/cm2 y a 28 días > 800 kgf/cm2.
Morteros con fibras sintéticas para mayor resistencia a la flexotracció (> 60 kgf/cm2 a 28 días).
Morteros tixotrópicos: Consistencia adecuada para trabajos en paramentos verticales y sobre cabeza sin correrse. La mayoría de los productos anteriormente mencionados poseen esta característica debido a su mayor contenido de finos(cemento, arna fina y microsílice) y aditivos.
Morteros autonivelantes: Morteros fluidos para aplicar en superficies horizontales (pisos).
Propiedades
Las propiedades específicas varían de un producto a otro y entre los distintos fabricantes.
En general están caracterizados por su elevada resistencia, rápido desarrollo de resistencia, buena adherencia y baja retracción.
3.4 Hormigónes
Cemento
Empleo de cemento Corriente o Alta Resistencia según requisitos de resistencia y velocidad de fraguado.
Áridos
Deben cumplir requisitos para empleo en hormigones de la norma NCh 163, especialmente composición granulométrica, resistencia y limpieza.
Morteros para grout o rellenos: Morteros fluidos, generalmente expansivos para aplicar bajo placas de anclaje de maquinarias o estructuras. Trabajos de inyecciones y rellenos en lugares estrechos.
Tamaño máximo: Compatible con espesores y densidad de armaduras de elementos a reparar.
En general, a falta de especificación se empleará una mezcla de arena y gravilla de tamaño máximo 20 mm (3/4”).
Agua
Potable y/o libre de substancias extrañas, sales disueltas o partículas en suspensión.
Dosificación
Según requisitos de resistencia y trabajabilidad especificados. A falta de especificación se empleará una dosis mínima de cemento de 340 kg/m3.
Aditivos
Pueden emplearse distintos productos según requisitos particulares necesarios, siendo de uso mas frecuente los plastificantes-reductores de agua, aceleradores y retardadores de fraguado, expansores, etc. Ver 3.5.
Resistencias Mecánicas: Igual o superior a la de la estructura que se vaya a reparar. En ningún caso la resistencia podrá ser inferior a 250 kgf/cm2.
Retracciones: Deberán ser lo más bajas posibles, lo que se obtiene con dosificación adecuada y mínima razón agua-cemento (a/c ≤ 0,45); obtención de trabajabilidad mediante aditivos plastificantes o fluidificantes, en volúmenes pequeños y confinados, emplear aditivo expansor.
Trabajabilidad: Generalmente se requieren hormigones de elevada docilidad, lo que se obtiene con aditivos plastificantes o fluidificantes.
Asentamiento de cono 12 a 24 cm.
Adherencia
Asegurar la unión íntima con los hormigones de la estructura.
Reparaciones estructurales: emplear puente de adherencia epóxico.
Reparaciones superficiales: emplear lechada con emulsión acrílica.
Confección, Colocación y Curado. Según prescripciones de NCh 170, extremando las precauciones en cada caso.
3.5 Aditivos para el Hormigón y Morteros
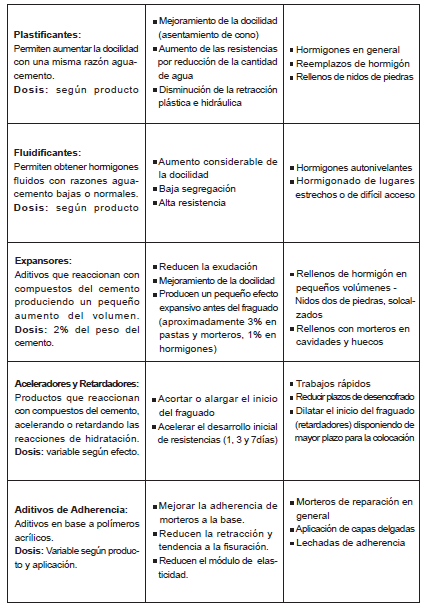
3.52 Sistemas Epóxicos
Productos de origen sintético que endurecen por reacción química entre una resina y un endurecedor.
Se entregan en 2 ó 3 componentes:
Parte A Resina
Parte B Endurecedor
Parte C Fillers o áridos.
Dosificaciones
Debe respetarse rigurosamente la proporción resina: endurecedor (A:B) indicada por el fabricante.
En la mayoría de los casos se emplean juegos completos predosificados.
La proporción de parte C (filler) puede ajustarse en obra según consistencia y propiedades requeridas.
Los sistemas epoxi, dependiendo de cada uso, podrán emplearse en forma de:
Líquidos más o menos viscosos según la formulación;
Pastas de consistencia espesa para lo cual se agrega polvo de cuarzo y eventualmente un agente tixotrópico;
Morteros epóxicos: agregando a la mezcla resina-endurecedor una arena, generalmente cuarzo, de una determinada granulometría.
Viscosidad
La viscosidad de los sistemas epoxi puros (sin filler) puede variar entre 100 y 2500 centipoise (cps) a 20°C, según la formulación. Para trabajos de inyección se requiere de productos de baja viscosidad. La viscosidad puede aumentarse con fillers para formar pastas tixotrópicas;
Velocidad de Reacción
Condiciona el pot-life o tiempo de endurecimiento inicial y el desarrollo de resistencia en plazos cortos. Depende de la formulación, temperatura y volúmenes de mezclas. En general se alcanzan altas resistencias a edades tempranas con posibilidades de puesta en servicio dentro de los 3 primeros días. Las reacciones son exotérmicas, lo que puede limitar los volúmenes a preparar.
Retracciones
Endurecimiento prácticamente sin retracción.
Propiedades mecánicas (a 7 días)
Resistencia a compresión 400 a 1 .000 kgf/cm2
Resistencia a flexotracción 200 a 800 kgf/cm2
Adherencia al acero sobre 200 kgf/cm2
Adherencia al hormigón sobre 50 kgf/cm2 (rotura del hormigón).
Módulo de elasticidad 10.000 a 350.000 kgf/cm2 (según formulación y contenido de filler).
Sensibilidad Térmica
La temperatura de aplicación influye sobre la viscosidad y velocidad de reacción.
Los cambios de temperatura posteriores intervienen en las deformaciones. El coeficiente de dilatación térmica varía de 4.5 a 6.5 x 10 -5 cm/cm ºC, valor que disminuye considerablemente con la adición de fillers.
Los fabricantes y proveedores ofrecen productos para distintas aplicaciones:
Productos tixotrópicos para sellado, adhesivo y trabajos sobre cabeza.
Puentes de adherencia: Adhesivos líquidos para la unión de hormigón fresco con hormigón endurecido.
Adhesivos para hormigones prefabricados, acero-hormigón, anclajes.
Adhesivo para pegar placas de refuerzo de acero o fibra de carbono.
Productos líquidos para anclajes, nivelación y rellenos bajo placas de maquinaria o estructuras (grouts).
Morteros de sellado y nivelación.
Productos de baja viscosidad para inyección de grietas.
3.53 Fibra de Carbono (FRP)
Sistema de alta tecnología utilizado como refuerzo exterior, alternativo al acero, por su gran resistencia a la tracción.
En general se emplean en forma de pletinas o tejidos de fibra de carbono.
Pletinas de Fibra de Carbono: Pletina de polímero reforzado con fibra de carbono de alta resistencia. Generalmente se presenta en espesor de 1,2 mm por 50 mm de ancho.
Su resistencia a la tracción es > 28.000 kg/cm2. Se adhiere al hormigón con un adhesivo epoxi.
Tejido de fibra de carbono de alta resistencia unidas con una resina epoxi: Se presenta en espesor del orden de 0,2 mm y un ancho de 30 o 60cm. Cono adhesivo al hormigón se emplea un sistema epoxi de impregnación
Estos sistemas son muy sofisticados y tanto el diseño del refuerzo como su aplicación y supervisión requieren de profesionales y personal calificados.