El curado del hormigón es un proceso imprescindible en la secuencia de construcción de una obra ya que mejora la durabilidad, al favorecer el aumento de la impermeabilidad, y el desarrollo de las propiedades mecánicas del hormigón. Las figuras IV.1 a IV.3 ilustran, de manera esquemática, la importancia de aplicar un curado adecuado a todos los elementos de una obra.
La Figura IV.1 muestra el efecto del tiempo de curado en la evolución de resistencia en probetas a las que se les ha retirado el curado húmedo a los 3 días y a los 7 días y otras que se han mantenido continuamente en condición de curado. Esta figura enfatiza, al igual que muchas otras que se encuentran en la literatura técnica, la gran importancia de un adecuado curado en obra desde el punto de vista de las resistencias mecánicas.
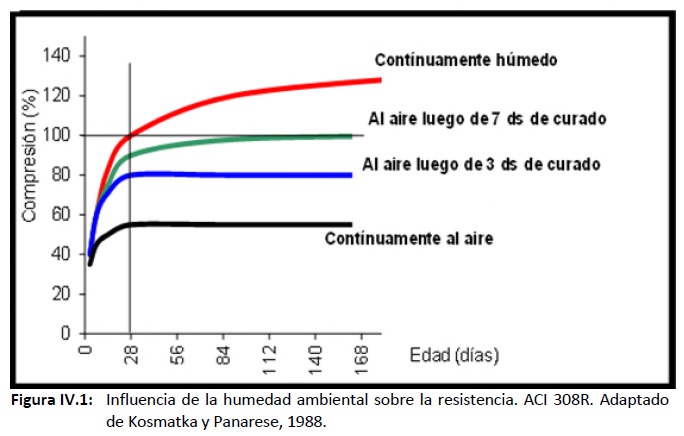
Por su parte, la Figura IV.2 remarca lo anterior, ilustrando esquemáticamente el significativo impacto que tiene el tipo de curado y el porcentaje de adiciones en la durabilidad del hormigón, expresada en función de la impermeabilidad. De esta figura es posible concluir que la mejor opción para aumentar la durabilidad del hormigón es aplicar un buen sistema de curado, por el período apropiado a la condición de exposición del elemento. Utilizar cementos con adiciones es una buena alternativa siempre y cuando se aplique un buen curado. Vale recordar que el proceso de reducción de poros que produce la reacción puzolánica, se produce si y sólo si hay humedad suficiente para que los materiales suplementarios del cemento reaccionen con el hidróxido de calcio para formar compuestos que poseen propiedades cementicias.
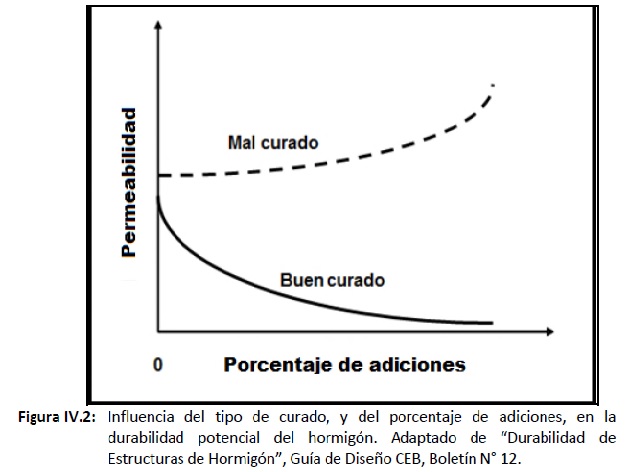
En resumen, aparte del requerimiento de resistencia mínima a compresión (potencial o real) para autorizar discontinuar el curado, sería altamente recomendable incluir y exigir en las especificaciones técnicas de una obra la ejecución de ensayos de impermeabilidad del hormigón, en aquellas situaciones en las que un constructor desee proponer sistemas de curado distintos a los que ha sancionado la práctica (Ver Sección II precedente).
Por último, la Figura IV.3 esquematiza la tasa de evaporación promedio a lo largo del año para las principales ciudades de Chile, notándose que ésta típicamente se ubica sobre el límite práctico aceptado de 0,5 kg/m2/h que marcaría el umbral a partir del cual aumenta el riesgo de aparición de fisuración por retracción plástica. Lo anterior muestra la importancia de aplicar un adecuado curado en toda la extensión del territorio nacional, durante todo el año.
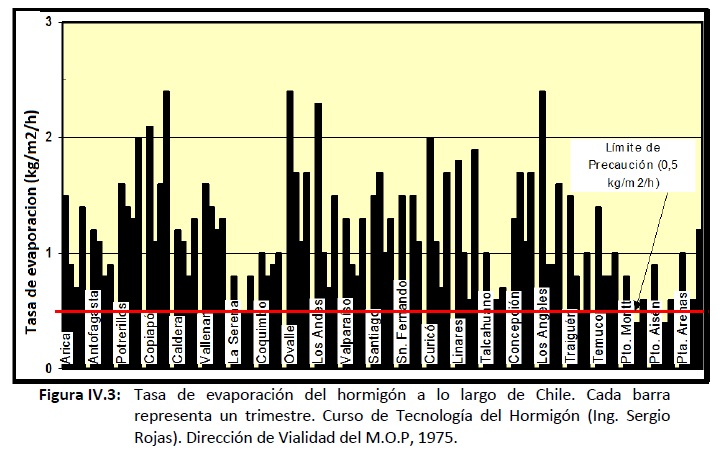
Establecida la importancia del curado del hormigón, se debe hacer notar que las exigencias de curado en una obra de hormigón están condicionadas, tanto por las características propias del material (grado del hormigón, razón agua-cemento, tipo de cemento, entre otras), como por el tipo de elemento, características geométricas de la sección, en términos de la relación volumen a superficie expuesta del elemento de hormigón, y las condiciones climáticas en las que la obra se emplaza.
Los requerimientos mínimos de curado, según NCh170:2016, son los siguientes:
a) Iniciar el curado tan pronto como las operaciones de colocación del hormigón lo permitan y/o las condiciones ambientales lo hagan necesario.
b) Mantener la humedad en la superficie del elemento por al menos 7 días si no se mide resistencia real del hormigón. Se debe verificar que la temperatura del hormigón colocado en obra no descienda de 5 °C durante ese período y que la temperatura promedio diaria no descienda de 10 °C en el mismo lapso de tiempo.
c) Hasta alcanzar una resistencia mínima real, es decir medida en un elemento en terreno, de al menos un 70% de la resistencia especificada, lo que se puede constatar, por ejemplo, mediante la aplicación del concepto de madurez. De no poder determinar dicha resistencia real, ya sea directa o indirectamente, la exigencia para la resistencia potencial, obtenida de probetas bajo condiciones normalizadas, es de alcanzar un 85% de la resistencia especificada, en virtud de la incerteza de su verdadera
representatividad de lo acontecido en el hormigón colocado en la estructura.
Si el proyecto espera condiciones de exposición muy severas, ya sea durante la construcción o en la vida de servicio de la estructura, entonces el curado debe extenderse hasta lograr el 100% de la resistencia especificada o lograr el nivel de impermeabilidad especificado en el proyecto y medido en terreno por algún método apropiado. En otras palabras, para asegurar durabilidad en estas condiciones desfavorables es posible que el curado deba extenderse por más de 7 días para lograr los objetivos antes planteados. Lo mismo ocurre si durante el período de curado el elemento queda expuesto a condiciones adversas de baja temperatura o humedad.
Se recomienda que el ingeniero diseñador revise y conozca las secciones 13.1
Generalidades; 13.2 Métodos y plazos de curado, en las cuales se indican alternativas de
métodos de curado y 13.3 Protección, de la norma NCh170:2016 al momento de realizar su
especificación de protección y curado del hormigón en obra y tenga en consideración que el
plazo de curado depende de la potencialidad de alcanzar la resistencia o durabilidad
(impermeabilidad) deseadas.
Para especificar métodos y materiales de curado se puede recurrir al documento ACI 308.1
y/o NCh170:2016, sección 13.2.
Una forma práctica de verificar si el periodo de curado en obra es adecuado, consiste en mantener probetas en obra curadas de manera equivalente al curado que se hace de la estructura, tal como lo señala ACI 318-14, en las secciones 26.5.3.2 (d) y (e). El curado se considerará satisfactorio si la resistencia promedio de las probetas curadas en sitio, conforme a ASTM C31, es al menos un 85% de la resistencia obtenida de las probetas hermanas que se mantuvieron en un curado estándar, o si la resistencia promedio de las probetas curadas en sitio excede en no menos de 3,5 MPa la resistencia especificada a la
edad de ensayo o de término del curado.
Alternativamente se puede evaluar la resistencia real del hormigón colocado en el elemento estructural por alguno de los métodos indicados en la sección X de esta guía como, por ejemplo, madurez.
Un claro síntoma de que el proceso de curado es insuficiente es la aparición de fisuras plásticas, particularmente en losas, las cuales son visibles dentro de las primeras 24 horas de colocado el hormigón.
Respecto de la influencia de distintas variables en el proceso de curado, se tiene:
I. Tipo de elemento: Las características del curado difieren principalmente entre losas y otros elementos debido a la mayor superficie expuesta, en relación al volumen del elemento estructural, que tienen las primeras. Esto es aún más crítico en radieres o losas apoyadas en el terreno, dado que la pérdida de humedad desde la masa de concreto ocurre tanto al ambiente como al terreno. Por tal motivo se recomienda tomar medidas para que ambas superficies se mantengan húmedas y pierdan humedad en
forma uniforme para evitar alabeos.
Elementos como muros, vigas, columnas o pilares, sufren de manera similar los efectos de la evaporación. Se recomienda humedecer (no saturar) las superficies interiores de los moldes y refuerzos previo al vaciado del hormigón y al retirar los moldes, aplicar alguno de los métodos de curado (membrana, láminas u otros) hasta alcanzar el tiempo de curado requerido para garantizar el logro de la resistencia y durabilidad especificadas en el diseño.
Respecto de este tipo de elementos, el Contratista deberá poner cuidado en aquellos elementos que están más expuestos al sol o viento, por su orientación dentro de la estructura, los que deberán contar con mayor protección.
Como nota adicional, respecto del moldaje, se debe señalar que, en el caso del uso de moldajes metálicos, el constructor debe considerar su alta conductividad térmica al momento de definir su plan de protección del hormigón.
II. Resistencia del hormigón: La resistencia del hormigón también es un factor a considerar en la especificación de las exigencias de curado. En la práctica en Chile, concretos que presentan una mayor resistencia cilíndrica especificada han tendido a ser menos susceptibles a sufrir los efectos de un curado deficiente, respecto de otros expuestos similarmente, pero de menor grado. Se hace notar, sin embargo, que no existen experiencias de investigaciones a este respecto que permitan establecer un grado o
valor de resistencia especificada límite.
III. Condiciones climáticas. Influyen aspectos como la temperatura ambiente y del hormigón
al momento de la colocación del hormigón, la humedad relativa del aire, velocidad del
viento y radiación directa del sol. Estas variables determinan la diferencia de presión de
vapor en la superficie del hormigón y la presión de vapor en el aire que lo circunda y
esta diferencia de presiones se puede relacionar con las temperaturas en ambas masas
de vapor, siendo la del agua en la superficie del hormigón típicamente aceptada como
igual a la temperatura superficial del hormigón. Por lo tanto, controlar la temperatura
superficial del hormigón colabora a disminuir la tasa de pérdida de humedad del mismo.
No hay un método preciso para estimar la inter-relación entre estas variables, sin embargo, la fórmula de Menzel (1954) y el nomograma de Bloom (1960) se consideran como un buen método para predecir cuándo se requiere adoptar un mayor cuidado en el curado del hormigón. No se debe considerar como un método para determinar la tasa de secado del hormigón. El nomograma citado relaciona temperatura ambiente, humedad relativa, temperatura superficial del hormigón y velocidad del viento. La norma NCh170:2016 establece como una condición de riesgo de fisuración del hormigón que la tasa de evaporación supere un valor por sobre 1 kg/m2/h. Se hace notar, sin embargo, que la experiencia práctica a nivel nacional indica que valores de la tasa de evaporación por sobre 0,5 kg/m2/h, durante o inmediatamente posterior a la colocación del hormigón, ya incrementan las probabilidades de aparición de fisuras por retracción plástica.
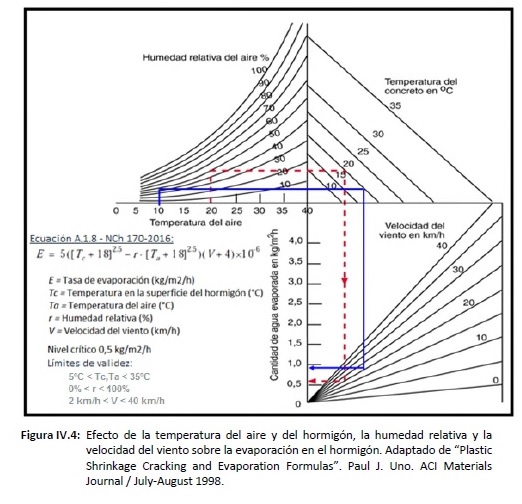
Cabe hacer notar que el riesgo de fisuración es mayor en el hormigón que aún no inicia su proceso de endurecimiento, es decir, durante las primeras horas posteriores al vaciado y terminación.
En relación a los procedimientos de curado, en sección 13.2.1 de NCh170:2016, se indican los que son viables de aplicar, recomendando el uso de agua nebulizada o lloviznas tenues de agua. Las membranas de curado son una alternativa que se pueden aplicar una vez que el hormigón tiene una resistencia suficiente para no dañarse durante la colocación. Dichas membranas deben poder ser aplicadas en superficies húmedas. Su uso debe restringirse a compuestos que certifiquen satisfacer ASTM C309 y ASTM C1315 y que además puedan colocarse antes que ocurra la pérdida de agua por exudación. Las ventajas del uso de aquellas que satisfacen ASTM C1315 es que siendo pigmentadas permiten detectar
fácilmente zonas no cubiertas. Dentro de las desventajas es que pueden afectar la apariencia final de la superficie o incluso impedir la adherencia de los sustratos de terminación (pintura u otros). En este sentido, aquellos que satisfacen ASTM C1315 promueven la adherencia de sustratos de terminación (cerámicas u otros). Cabe indicar que la eficacia de estos sistemas depende de las condiciones de terreno y, en particular, de la textura de la superficie del elemento de hormigón. Elementos de superficies rugosas
requerirán mayor cantidad del compuesto para lograr un curado efectivo. Es así como es recomendable evaluar si el método seleccionado es realmente efectivo para evitar fisuras plásticas. Un procedimiento que ha resultado ser exitoso para evaluar la efectividad de las membranas, es realizar el ensayo ASTM C309 sobre probetas extras a las que se les aplica la membrana inmediatamente después de fabricadas y se les exigen los mismos límites que las del ensayo ASTM C309. Si no cumplen estos límites se deberá redefinir el método de curado seleccionado hasta lograr cumplir lo exigido por ASTM C309.
La Tabla IV.2 muestra la máxima pérdida de agua admisible para una membrana de acuerdo a los requisitos del estándar ASTM C309 y del código ACI 350R, este último, para obras hidráulicas.
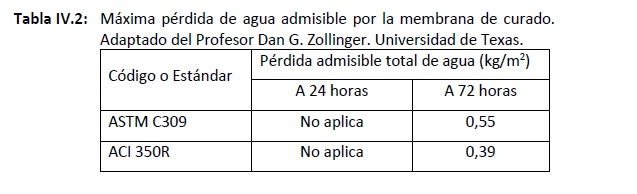
Referencias:
- ACI 308.1-11. Specification for Curing Concrete.
- ACI 350-06. Code Requirements for Environmental Engineering Concrete Structures and Commentary.
- ASTM C309. Standard Specification for Liquid Membrane-Forming Compounds for Curing Concrete.
- ASTM C1315. Standard Specification for Liquid Membrane-Forming Compounds Having Special Properties for Curing and Sealing Concrete
- Evaluación de la Aplicabilidad de Ensayos No Destructivos para el Control de Calidad del Hormigón. Hernán Ferreira J. Tesis para optar al grado de Magister en Ciencias de la Ingeniería. Pontificia Universidad Católica de Chile. Septiembre 2004.
- STAR 230-DUC. Performance Based Specifications and Control of Concrete Durability. RILEM.
- Menzel, C.A. “Causes and Prevention of Crack Development in Plastic Concrete”. Portland Cement Association Annual Meeting, 1954.
- Bloem, D. “Plastic Cracking of Concrete”. Engineering Information, National Ready Mixed Concrete Association / National Sand and Gravel Association, July 1960.
- Zabaleta, H. Tecnología de la Construcción en Hormigón, Julio 2003.