2.1 Bloques de Hormigón.
Las Normas Chilenas han establecido en NCh 1928, “Albañilerías Armadas: Requisitos para el
Diseño y Cálculo”, las condiciones mínimas que deben cumplir los bloques huecos de hormigón
para su empleo en construcciones de albañilería armada.
Estas condiciones se relacionan con las estipulaciones generales para bloques de hormigón
contenidas en NCh 181, “Bloques Huecos de Hormigón de Cemento”, y su conjunto puede
desglosarse y resumirse en la forma que se detalla a continuación:
a. Dimensiones de los bloques.
Las dimensiones básicas de los bloques huecos deben atenerse a la siguiente pauta:
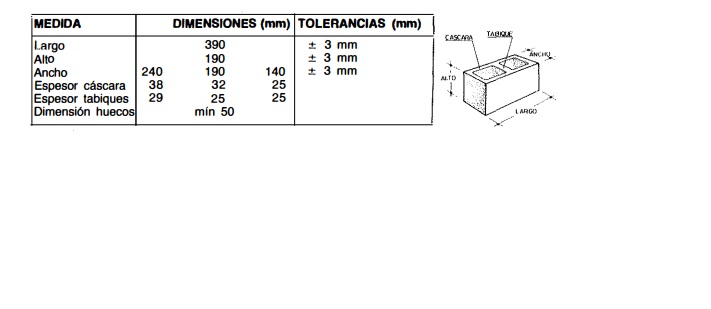
La Norma establece, además, otras condiciones de medidas para los bloques constituidos por
cáscaras compuestas, las cuales no se incluyen por tratarse de elementos no empleados en
nuestro Pais.
Otras dimensiones, distintas de las normalizadas, pueden ser convenidas entre comprador y
suministrador, siempre que se cumplan con las tolerancias y requisitos establecidos en la norma.
b. Resistencia.
La resistencia mínima a compresión de los bloques empleados en albañilerías armadas debe ser
de 5.0 MPa ( aproximadamente 50 kg/cm2). La Norma establece para ella una fracción defectuosa de 4%, valor que debe ser ratificado por el Proyectista.
c. Absorción y Humedad.
La Norma NCh 181 establece que la absorción de los bloques no debe exceder de 240 Kg/m3 de
hormigón. La Norma NCh 1928 define que para la albañilería armada este valor es válido cuando la
densidad del hormigón del bloque está comprendida entre 1700 y 2000 Kg/m3
, pudiendo aumentarse a 290 Kg/m3 de hormigón si la densidad de este último es inferior a 1700 Kglm3 y debiendo
reducirse a 21 O Kg/m3 si su densidad es mayor que 2000 Kg/m3
.
Es conveniente señalar que este último valor constituye un límite bastante exigente, puesto que
dicho valor de absorción corresponde a 100% de la porosidad contenida en un hormigón para
bloque con una dosificación muy cuidadosa. De manera que su cumplimiento obliga al empleo de
una tecnología apropiada.
Por su parte, la humedad de los bloques en el momento de su entrega en obra debe limitarse a un
valor máximo de un 40% de la absorción media medida para un mínimo de tres bloques.
En relación con esta exigencia, es necesario comentar que su cumplimiento debe ser analizado en
relación con la humedad relativa media existente en el lugar de la obra, puesto que su cumplimiento
estricto en los puntos en que la higrometría es muy alta puede ser difícil de obtener, obligando a
largos plazos de mantención en secado de los bloques.
Por este motivo, en estos casos debe analizarse también el valor de humedad que corresponde al
equilibrio con la humedad media del lugar.
Estos límites de absorción y humedad son importantes desde el punto de vista del control de la
contracción de los bloques producida por variaciones de humedad una vez colocados éstos en la
albañilería.
Por este motivo, la Norma NCh 1928 señala que cuando en un Proyecto deban exigirse
limitaciones especiales de la retracción lineal, la humedad debe cumplir las condiciones especificadas en la Norma ASTM C 90. Esta Norma establece que, de acuerdo al valor de retracción
lineal que estime necesario exigir el Proyectista y a las condiciones de humedad del sitio de la
obra, la humedad máxima de los bloques no debe exceder de los valores que se tabulan a
continuación:
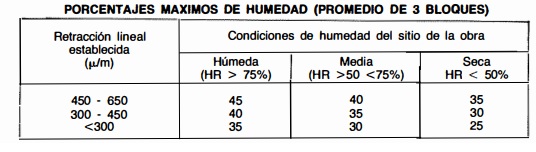
A título informativo se incluyen en forma resumida las condiciones exigidas para los ladrillos
cerámicos que se utilicen en albañilerías armadas, en la Tabla siguiente:
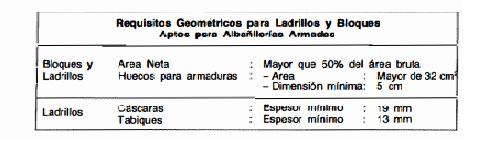
d. Otras características no normalizadas.
- Aislación térmica.
La aislación térmica de un material determinado puede medirse por medio de sus coeficientes de
transmisibilidad U y resistencia térmica R.
El primero mide la cantidad de calor que es capaz de circular por unidad de superficie, de tiempo
y de diferencia de temperatura entre las caras caliente y fría del elemento.
La resistencia térmica se calcula como el valor recíproco de la transmisibilidad. Presenta con
respecto a ésta la ventaja de que en elementos compuestos de materiales distintos, la resistencia total puede calcularse como la suma de las resistencias individuales de los componentes.
Ensayos efectuados en EEUU sobre bloques de dimensiones y densidad similares a los
producidos en nuestro país indican valores de R como los que aparecen en la tabla que se
inserta posteriormente. Estos valores varían significativamente con la densidad del hormigón de
los bloques y especialmente si los huecos de los bloques se rellenan con mortero u hormigón
liviano. A título indicativo, se anotan en la misma tabla los valores para bloques de densidad igual
a la mitad de la del hormigón convencional y para bloques con densidad normal, pero con relleno
de mortero liviano en sus huecos:
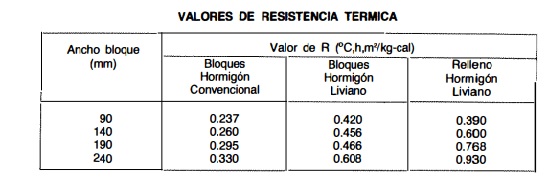
Los valores indicados para el bloque de hormigón convencional son similares a los posibles de
obtener con un muro de ladrillo del mismo espesor, con la ventaja adicional para el bloque de
aumentar significativamente su capacidad aislante mediante un relleno de material liviano.
- Aislación acústica.
La determinación de la calidad de aislación acústica de un material se relaciona con su
capacidad de absorción de energía y de intensidad de las ondas acústicas.
La absorción de energía acústica se mide en función de la pérdida de energía de las ondas
sonoras emitidas junto a una pared en relación a la recibida en la cara opuesta. Esta pérdida de
energía se expresa como un coeficiente que relaciona dicha pérdida con la que se experimenta
en una superficie totalmente absorbente y, dado que depende de la frecuencia del sonido, se
acostumbra medirla como el promedio de los coeficientes de absorción obtenidos para frecuencias de 250, 500, 1000 y 2000 Hz.
La pérdida de intensidad de las ondas acústicas se mide a través de la variación de su presión,
expresada en decibeles, entre las caras opuestas de la pared desde el punto de emisión y el de
recepción.
Para muros de bloques de hormigón convencional, de espesor de alrededor de 20 cm, estos
parámetros tienen los valores aproximados que so indican a continuación: - Coeficiente de absorción de energía acústica : 0.27 ( aprox 1.5db )
- Coeficiente de pérdida de intensidad acústica: 50 db
Las cifras anteriores indican que los muros de bloques de hormigón alcanzan una mayor
efectividad en lo que concierne a pérdida de intensidad acústica que para la absorción de
energía acústica.
Ello significa que aislan mejor la transmisión de sonidos a través de su espesor, siendo, en
cambio, menos efectivos para absorber los sonidos que se producen en el interior de una
habitación.
Por otra parte, los valores señalados para el primero de estos parámetros son comparables con
los recomendados como aceptables para muros divisorios entre viviendas contiguas, por lo que
los muros divisorios en base a bloques de hormigón son apropiados desde el punto de vista de
su aislación acústica.
En lo concerniente a los valores señalados para la absorción acústica, aun cuando son relativamente bajos, puede señalarse que son equivalentes a los de otros materiales empleados con
fines similares en la construcción (ladrillos cerámicos, madera).
Por otra parte, dado que adicionalmente a las características de los materiales, debe considerarse la influencia de otros factores que condicionan fuertemente el nivel de absorción acústica, - entre los cuales pueden seiialarse las mejoras producidas por la aplicación de recubrimientos
- (pinturas, enlucidos o similares ) o de los elementos decorativos normalmente usados en las
- habitaciones (alfombras, cortinas), los valores básicos seiialados no son de gran importancia,
- puesto que pueden ser variados fácilmente por factores externos cuya influencia es muy
- significativa.
- Resistencia al fuego.
La resistencia al fuego de un material se determina mediante un ensayo que consiste en someter
una muestra a un ciclo normalizado de temperaturas, con un máximo de 1200ºC, en un horno de
temperatura controlada.
Se evalúa a través del tiempo necesario para el cumplimiento de cualquiera de las tres
condicionas siguiontos: - falla estructural bajo la carga de diseno
- elevación máxima de temperatura producida por la transmisión de calor, considerándose como máximo aceptable una elevación media de 121 ºC o una local de 163ºC
- paso de llamas o gases calientes
Con fines comparativos entre distintos tipos de materiales, se acostumbra expresar su resistencia al fuego en función de un factor denominado espesor equivalente. Este se define como el
espesor de material sólido existente en el camino del flujo calórico, necesario para que se
produzca la elevación máxima de temperatura aceptada en el ensayo de resistencia al fuego en
un determinado lapso de tiempo.
El espesor equivalente para muros construidos con bloques de hormigón puede estimarse a
partir de los valores que se indican en la siguiente tabla:

Considerando el espesor sólido de los tabiques que constituyen un bloque, estas cifras indican
que la resistencia al fuego de un muro simple de albañilería de bloques alcanza valores similares
a una hora.
Los valores indicados pueden aumentarse significativamente si se procede a rellenar los
espacios huecos de los bloques, caso en el cual su resistencia al fuego puede estimarse que
aumentará a los siguientes valores:

En consecuencia, puede suponerse que los muros de albañilería armada, aun cuando sólo
tienen un relleno parcial de su volumen, presentan una aceptable resistencia al fuego, debiendo
procederse a un relleno total en aquellos muros en que se desee una elevada seguridad.
2.2 Morteros de Junta.
Los bloques constituyentes de una albañilería se adhieren entre sí mediante un mortero de
cemento Este mortero debe desempeñar adecuadamente las funciones que le corresponden y
que, en líneas generales, son las siguientes:
- producir la adherencia entre bloques a fin de que trabajen en forma monolítica
- sellar las juntas entre bloques,
- compensar las diferencias de dimensiones existentes entre bloques
El mortero es utilizado, además, para proporcionar terminaciones arquitectónicas al ser trabajado mediante herramientas adecuadas para este objeto.
Para obtener estas propiedades el mortero debe poseer ciertas condiciones mínimas de trabajabilidad, adherencia y resistencia, que deben ser estudiadas convenientemente, para lo cual
existen ciertas reglas y principios mínimos, que se resumirán en los párrafos que siguen.
a. Trabajabilidad.
El mortero debe tener una trabajabilidad tal que se extienda con facilidad y cubra la superficie de
los bloques que se van a adherir entre si, sin escurrir excesivamente al ser presionado por éstos
durante su colocación. Lo anterior implica una fluidez y consistencia apropiadas para este objeto,
las que deben ser obtenidas mediante una cantidad conveniente de agua y una granulometría
apropiada de los materiales sólidos (arena, cemento y eventualmente adiciones).
En general, esta trabajabilidad no puede ser obtenida sin la adición de un material fino, para lo que
normalmente se usa la cal hidráulica, en la forma que se analizará posteriormente.
b. Adherencia.
La adherencia del mortero está destinada a producir la ligazón mecánica entre los bloques
componentes de la albañilería. La adherencia del mortero debe ser estudiada tanto a través de
sus propiedades en estado fresco como endurecido.
En la primera condición, la adherencia se relaciona con la retentividad de agua del mortero. Esta
influye en dos formas, por una parte, precaviendo la rigidización de la mezcla, derivada de la
absorción de agua por parte del bloque inferior, y por otra, reduciendo la exudación, que conduce a
una junta débil entre el mortero y el bloque superior.
Para obtener la retentividad apropiada, debe emplearse una proporción adecuada de granos finos,
de manera que también en este caso puede ser conveniente la adición de cal hidráulica.
En el estado endurecido, la adherencia está directamente relacionada con la resistencia mecánica del mortero, que puede medirse a través de su resistencia a la compresión.
En consecuencia, para una adecuada adherencia del mortero debe considerarse simultáneamente una proporción conveniente de granos finos y una resistencia a la compresión apropiada a
las características da la albañilería de la que forma parto constituyente.
c. Resistencia.
La resistencia del mortero de junta es necesaria tanto del punto de vista de la adherencia, como
para asegurar que la albañilería de la que forma parte tenga la resistencia prevista.
En base a los principios generales expuestos en los párrafos anteriores, en las líneas que siguen
se presentarán las reglas y criterios que han sido normalizados o que la práctica ha sancionado
como aplicables para evaluar las características y determinar las proporciones de los componentes del mortero, de manera que éste cumpla en forma adecuada las funciones descritas y,
además, los procedimientos para determinar si las propiedades obtenidas en el mortero así
preparado son efectivamente las previstas.
2.2.1 Condiciones de los componentes del mortero.
a. Cemento.
Para la confección de los morteros de junta puede utilizarse cualquiera de los tipos de cemento
nacionales existentes en el mercado. Sin embargo, son generalmente preferibles los cementos
del tipo corriente sobre los de alta resistencia, ya que a su menor costo unen la característica de
ser de fraguado más lento, lo cual permite un mayor tiempo de empleo en obra sin perder la
trabajabilidad de la mezcla en estado fresco.
b. Áridos.
La práctica habitual en nuestro país es utilizar un solo árido, de granulometría fina (arena). Este
árido deberá cumplir los mismos requisitos generales establecidas para los áridos para hormigones en la Norma NCh 163, las cuales pueden resumirse como se indica:
i) Contenido máximo en peso de material lino inferior a 0.080 mm: 3%
ii) Contenido de impurezas orgánicas inferior al correspondiente al color límite amarillo
claro del patrón standard definido en NCh 167.
iii) Contenido de sales solubles:
-sulfatos: inferior a 600 g /m3 de mortero
-sulfuros: inferior a 1800 g /m3 de mortero
IV) Pérdida de peso por desintegración por sulfato de sodio (magnesio): 10% (15%)
v) Contenido máximo en peso de carbón y lignito: 1 %
vi) Absorción máxima de agua en peso: 3%
En lo que concierne a su granulometría, la Norma NCh 1928 recomienda que ella quede
comprendida en la banda definida por los siguientes límites:
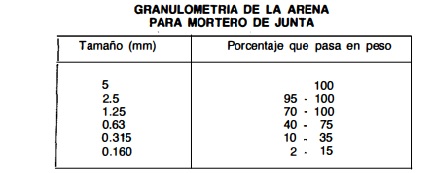
Es conveniente observar que las granulometrías extremas de la banda conducen a módulos de
finura comprendidos entre 1. 75 y 2.83, es decir más finas que lo habitual para la confección de
hormigones.
c. Agua.
El agua para los morteros de junta debe cumplir las mismas condiciones establecidas para el
agua empleada en la confección de hormigones, las cuales están definidas en la Norma NCh
1498 y pueden resumirse en la forma que se indica a continuación:
- El empleo de agua potable es aceptable sin análisis de verificación.
- No pueden emplearse aguas con contenidos de azúcares (sacarosa o glucosa).
- Las aguas desconocidas deben ser sometidas a análisis químico, debiendo cumplir los
siguientes requisitos mínimos:
• pH comprendido entre 6 y 9.2
• contenido de sólidos en suspensión inferior a 2000 mg/I
• contenido de sólidos disueltos inferior a 15000 mg/I:
• si el contenido de sólidos disueltos es superior a 5000 mg/I, el contenido de sulfatos,
expresado como SO, debe ser inferior a 600 g/m’ de mortero
• contenido de materias orgánicas inferior a 5 mg/I
d. Aditivos y Adiciones.
Se consideran como aditivos aquellos productos que añadidos en pequeña proporción en el
mortero modifican algunas de sus características . Su gama es muy variada, incluyendo entre
otros los plastificadores, aceleradores, retardadores, incorporadores de aire, impermeabilizantes, expansores etc.
Su empleo debe considerarse sólo en casos especiales, ya que normalmente el mortero puede
cumplir satisfactoriamente las condiciones,previstas sin utilizarlos, En el caso de recurrir a su
uso, es conveniente solicitar información al Proveedor respecto de sus características y de los
ensayos de laboratorio efectuados para verificarlas y para determinar sus proporciones de uso o,
en caso de no existir esos antecedentes, someterlos a ensayo para determinar su aplicabilidad.
Debe señalarse que un aditivo cuyo uso puede resultar conveniente para mejorar la consistencia
del mortero es el incorporador de aire. Sin embargo, debe recordarse que su empleo produce una
reducción de la resistencia, la que debe ser compensada aumentando la dosis de cemento.
Por cuanto hasta la fecha no existen Normas nacionales para aditivos, pueden emplearse como
referencia para este objeto las Normas ASTM C 494 y C 260.
Las adiciones están constituidas por materiales, generalmente sólidos, utilizados en proporciones similares a las de los componentes normales del mortero. Están dirigidas a modificar
algunas propiedades del mortero, principalmente su cohesión (consistencia), su retentividad y
eventualmente su color.
El material mayormente utilizado para este objeto es la cal hidratada en sus formas hidráulica o
aérea, cuyas especificaciones químicas y físicas aparecen detalladas en NCh 1928. De estas
estipulaciones conviene destacar las siguientes, por permitir apreciar en un caso particular la
calidad de la cal a utilizar:
- Porcentaje máximo de material de tamaño superior a 0.080 mm según NCh 150:
• Cal aérea: 1 O % • Cal hidráulica: 15 % - Retentividad según ASTM C 91:
• Cal aérea: 85 % • Cal hidráulica: 75 %
Debe señalarse que el empleo de cal hidratada debe efectuarse como adición y no como sustitución
de una parte del cemento, de manera de aprovechar su capacidad de aumento de la retentividad y
consistencia del mortero, evitando una disminución de la resistencia.
Las adiciones para colorear el mortero están normalmente constituidas por pigmentos granulares
de granulometría muy fina. Su empleo debe ser verificado mediante ensayos de laboratorio, si no
se dispone de antecedentes de empleo anteriores en condiciones similares, pues pueden
producir disminución de resistencia.
2.2.2 Dosificación de los Morteros de Junta.
El mortero de junta debe dosificarse para cumplir principalmente las condiciones de trabajabilidad y resistencia previstas. Una apropiada dosificación que contemple dichos factores permite
adicionalmente obtener una retentividad y durabilidad adecuadas, ya que estos últimos están
fuertemente relacionados con íos primeros.
La trabajabilidad debe determinarse de manera que el mortero cumpla las siguientes condiciones: - capacidad de sustentación en superficies verticales
- fluidez adecuada para un fácil esparcido, pero sin que escurra al colocar las hiladas
sucesivas sobre él
Como elementos para medir la trabajabilidad se ha utilizado normalmente la mesa de sacudidas
según ASTM C 230, estableciéndose para este patrón de medida un valor de 130 % como
aceptable para la fluidez de un mortero de junta. Paralelamente, también se ha empleado el
asentamiento en el cono de Abrams para este mismo objeto, indicándose en este caso valores
de 5 a 7 cm como aceptables.
Sin embargo, dado que las condiciones de trabajabilidad son diflciles de medir mediante ensayos
de laboratorio, deben ser apreciadas directamente sobre el mortero preparado, aspecto en el
cual la experiencia del albañil que utilizará el mortero es un importante elemento de juicio. Lo
anterior implica la necesidad de preparar mezclas de prueba para la adecuada verificación de
esta importante propiedad.
Posteriormente, al hablar de los Procedimientos Constructivos, se indicará una forma práctica de
evaluar esta característica, mediante el empleo de la plana del albañil.
En lo que concierne a la resistencia a compresión del mortero, NCh1928 especifica un valor
mínimo de 10 MPa (100 kg/cm2), medido en probetas de 4x4x16 cm.
Tornando en consideración lo expuesto, se estima que un criterio adecuado consiste en fijar una
resistencia de dosificación de 15 MPa (150 kg/cm2) a 28 días.
En base al criterio expuesto es posible definir en forma estimativa la dosificación de un mortero
de junta, con una fluidez aproximada en 5 cm de asentamiento do cono, do acuerdo a la Tabla
que se inserta a continuación:
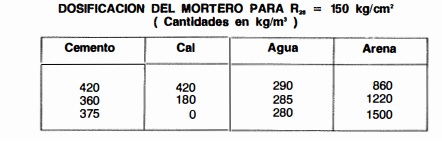
2.3 Morteros y Hormigones de Relleno.
Los huecos do los bloques en que van colocadas las armaduras deben ser rellenados mediante
hormigón o mortero. Este relleno permite, además de aumentar su resistencia, mejorar otras
propiedades, tales como su aislación térmica y acústica, su resistencia al fuego, etc.
Para lograr su . objetivo, el material de relleno debe tener las condiciones de trabajabilidad y
resistencia compatibles con la obtención del relleno total de los espacios en que va colocado y
con el rol estructural de la albañilería de que forma parte.
Más adelante, se verá la forma de obtener un adecuado cumplimiento de estas condiciones.
2.3.1 Condiciones de los Componentes de los Morteros y Hormigones de Relleno.
a. Cemento.
Las condiciones que debe cumplir el cemento son similares a las indicadas en 2.2.1 a) para los
morteros de junta. Sin embargo, en algunos casos particulares puede resultar conveniente el
empleo de cementos de alta resistencia, aspecto que deberá evaluarse de acuerdo al programa
de construcción previsto y las exigencias del proyecto estructural.
b. Áridos.
Los áridos cumplirán en general las condiciones especificadas en NCh 163 y que se resumieron
en 2.2.1 b). Deben agregarse a lo allí señalado las pertinentes al árido grueso, en caso de
preverse su utilización, y modificar las condiciones de granulometría señaladas para el árido fino
Estas condiciones adicionales o modificatorias pueden resumirse como sigue:
- Requisitos generales del árido grueso:
• Contenido máximo en peso de material fino inferior a 0.080 mm: 1.0 %
• Pérdida de peso por desintegración mediante sulfato de sodio (magnesio): 12 % (18%)
• Absorción máxima de agua en peso: 2 % - Requisitos de granulometría:
La granulometría de los áridos deberá quedar comprendida dentro de la siguiente banda
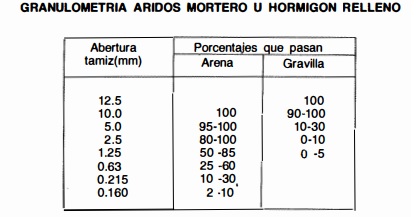
c. Agua.
El agua para los morteros y hormigones de relleno deberá cumplir las mismas condiciones
señaladas en 2.2.1 c).
d. Aditivos.
Para el empleo de aditivos en los morteros y hormigones de relleno se pueden seguir las mismas
pautas señaladas en 2.2.1 d).
Cabe hacer notar, sin embargo, que puede resultar conveniente prever el empleo de un aditivo
plastificador o superplastificador, pues permiten una mayor facilidad de control de la regularidad
de la fluidez de estos materiales.
2.3.2 Dosificación de los Morteros y Hormigones de Relleno.
Los morteros y hormigones de relleno cumplen una función especifica y totalmente diferente de
la del mortero de junta, por lo tanto estos últimos no deben ser utilizados en reemplazo de los
primeros.
Los morteros y hormigones de relleno deben dosificarse de manera que tengan una adecuada
trabajabilidad para su colocación en los espacios generalmente pequeños que quedan en el
interior de las albañilerías de bloque y para que puedan ser adecuadamente comp11ctados en su
sitio de colocación, ya sea en forma manual o mediante vibradores de inmersión de pequeño
diámetro.
Por las razones anteriores, el tamaño máximo del árido más grueso debe ser adecuado a la
menor dimensión de los espacios huecos que quedan en el interior de las albañilerías. Este
aspecto no ha sido hasta la fecha totalmente reglamentado, estimándose que dicho tamaño
máximo deberla limitarse a un valor comprendido entre 1/3 y 1/5 de la menor dimensión del
espacio libre a rellenar.
Adicionalmente, para lograr un buen llenado de los huecos es conveniente que el material de
relleno tenga una fluidez apropiada a la dimensión de los espacios a rellenar. Dado que ésta es
habitualmente pequeña y de acceso relativamente difícil, es conveniente que dicha fluidez sea
alta, estimándose apropiados unos 13 a 18 cm de asentamiento en el cono de Abrams cuando el
material se compacta por vibración y 15 a 20 cm cuando se utiliza varillado para este objeto.
Esta alta fluidez no debe ser obstáculo para que el material de relleno tenga la resistencia
prevista, la cual para albañilerías armadas ha sido establecida en un mínimo de 1 7.5 MPa (175
kg/cm2) medida a 28 días en cubo de 20 cm de arista.
Para determinar la dosificación de los morteros pueden utilizarse en primera aproximación las
cantidades que se indican en la tabla siguiente, estimadas para un mortero de razón cemento/arena 1 /3 en peso, que se considera apropiada para los morteros de relleno:
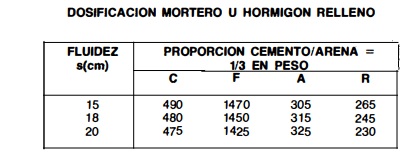
NOMENCLATURA:
s : fluidez medida mediante el asentamiento de cono
e : dosis de cemento en kg/m3
F : dosis de arena en kg/m3
A : dosis de agua en I/m3
R : resistencia estimada a 28 días en cubo de 20 cm de arista para obtener la resistencia
especificada
En el caso de utilizarse un relleno mediante hormigón, para su dosificación es conveniente
emplear un método de dosificación suficientemente probado en la práctica. Para este objeto en
el ANEXO 1 se incluye una versión simplificada del Método de Dosificación del American
Concrete lnstitute (ACI).
2.4 Armaduras.
Las barras de acero utilizadas en conexión con las albañilerías de bloques huecos de hormigón
son fundamentalmente de tres tipos:
a. Barras de Acero Estructural.
Están constituidas por barras que cumplen la Norma NCh 204, las cuales son usadas para las
siguientes funciones:
- armaduras resistentes, cuya cuantía y distribución se determina mediante cálculo
- armaduras de repartición, para la absorción de efectos secundarios, principalmente la
retracción hidráulica y térmica - armaduras horizontales para absorción del esfuerzo de corte en forma de escalerillas
- armaduras locales para absorción de efectos concentrados en puntos singulares (huecos de ventanas y puertas, etc.)
- b. Mallas Preformadas.
Son mallas prefabricadas que cumplen la Norma NCh 218, y se utilizan principalmente como
armaduras horizontales para absorción del esfuerzo de corte en forma de escalerillas y como
armadura de ligazón.
c. Pletinas.
Están constituidas por láminas metálicas de acero estructural, que se emplean como armaduras
de ligazón.
En el Capitulo 3 se analiza más en detalle la forma en que deben disponerse para cumplir las
funciones señaladas.
Independientemente de sus condiciones particulares, ellas deben cumplir condiciones generales
que se refieren con el estricto respeto de las calidades y dimensiones establecidas en el
Proyecto y con una adecuada limpieza previamente a su puesta en obra.
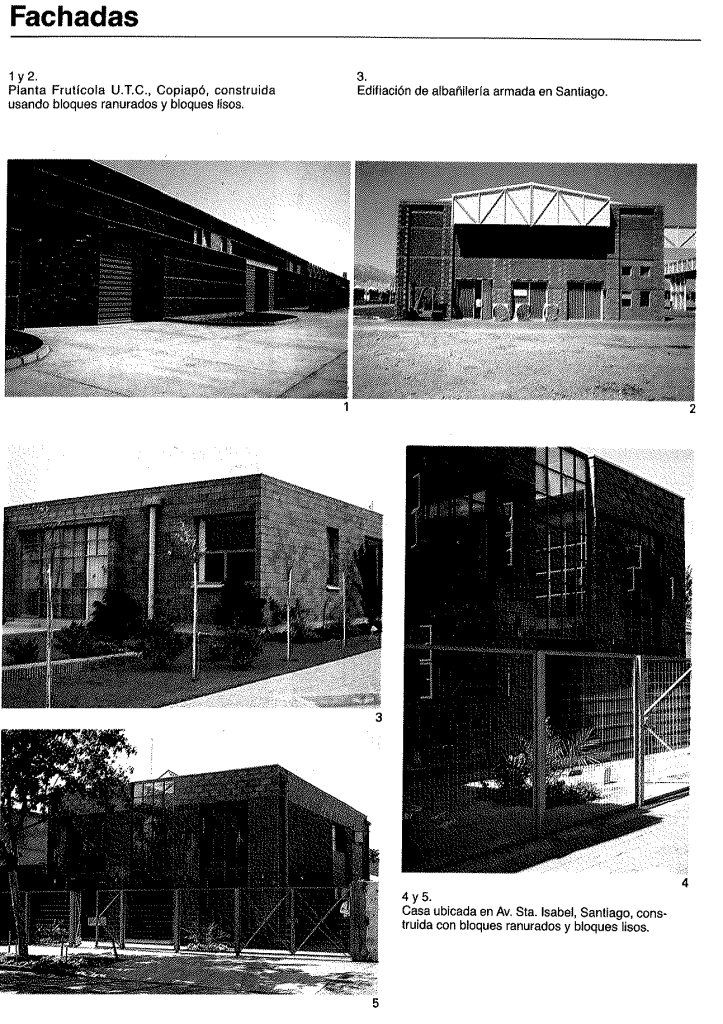
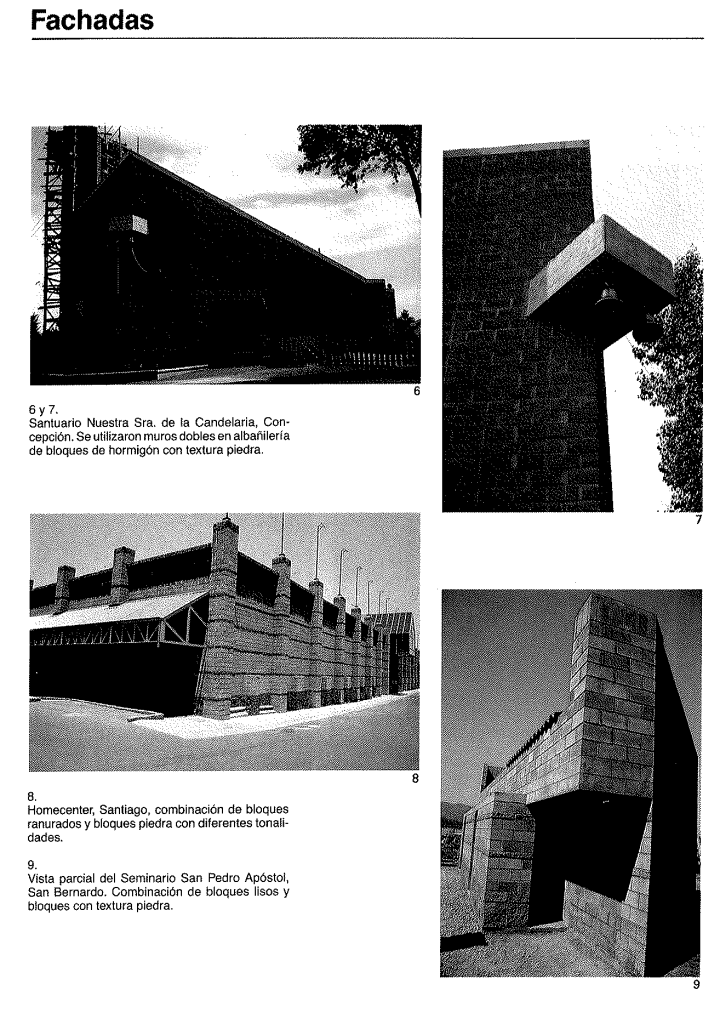