Somos el Instituto del cemento y del hormigón de chile
Hormigón
Nuestro presente
nuestro futuro
¡Descubre el hormigón, el material que construye tu mundo! Desde hogares acogedores hasta impresionantes rascacielos, este material versátil lo hace todo. Crea carreteras seguras, escuelas modernas y ciudades enteras, moldeando nuestro futuro sostenible. Pero no solo construye, ¡también protege! El hormigón es nuestro aliado contra el cambio climático, ofreciendo durabilidad incomparable. Además, impulsa la economía creando empleos y oportunidades.
Muchas Gracias
Ya estas inscrito en nuestra lista, recibirás toda la información que tenemos para ti
Últimas Noticias
Entérate de todo el mundo de la construcción con hormigón
Biblioteca ICH
Conoce las publicaciones del ICH
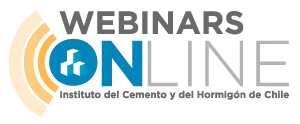
Te invitamos a ver nuestros webinar
Visualiza lo último en tendencias en el mundo de la construcción con hormigón
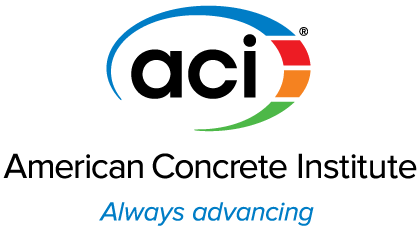
Visualiza ahora los Destacados ACI
Aqui recopilamos las mejores conferencias presentadas en las convenciones de la ACI
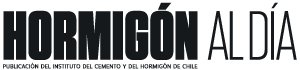
Visualiza ahora los Destacados HAD
Aquí recopilamos los últimos árticulos de nuestra revista Hormigón al Día
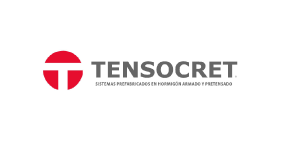
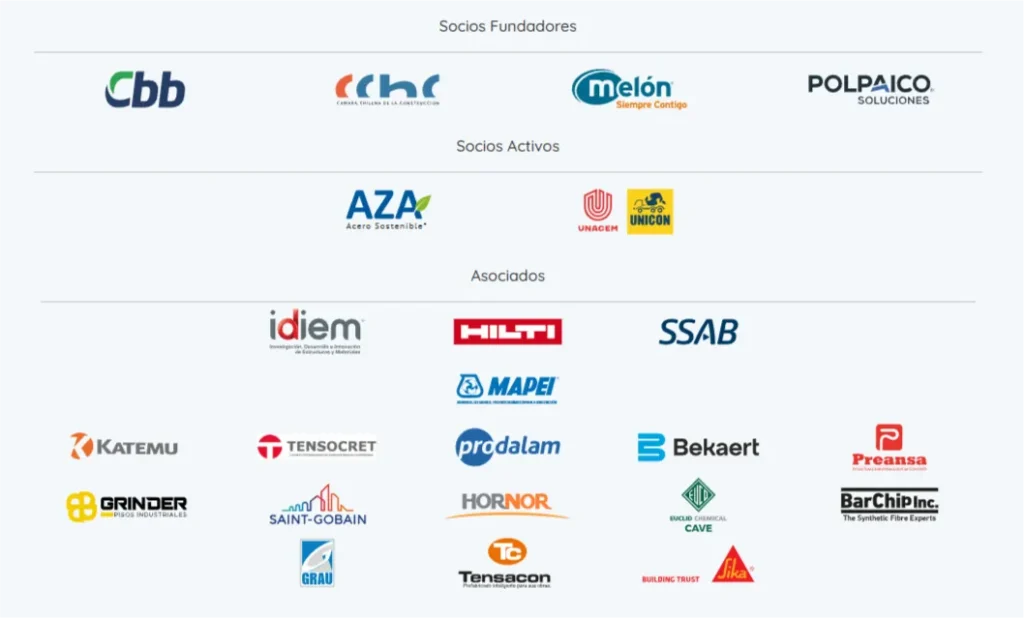